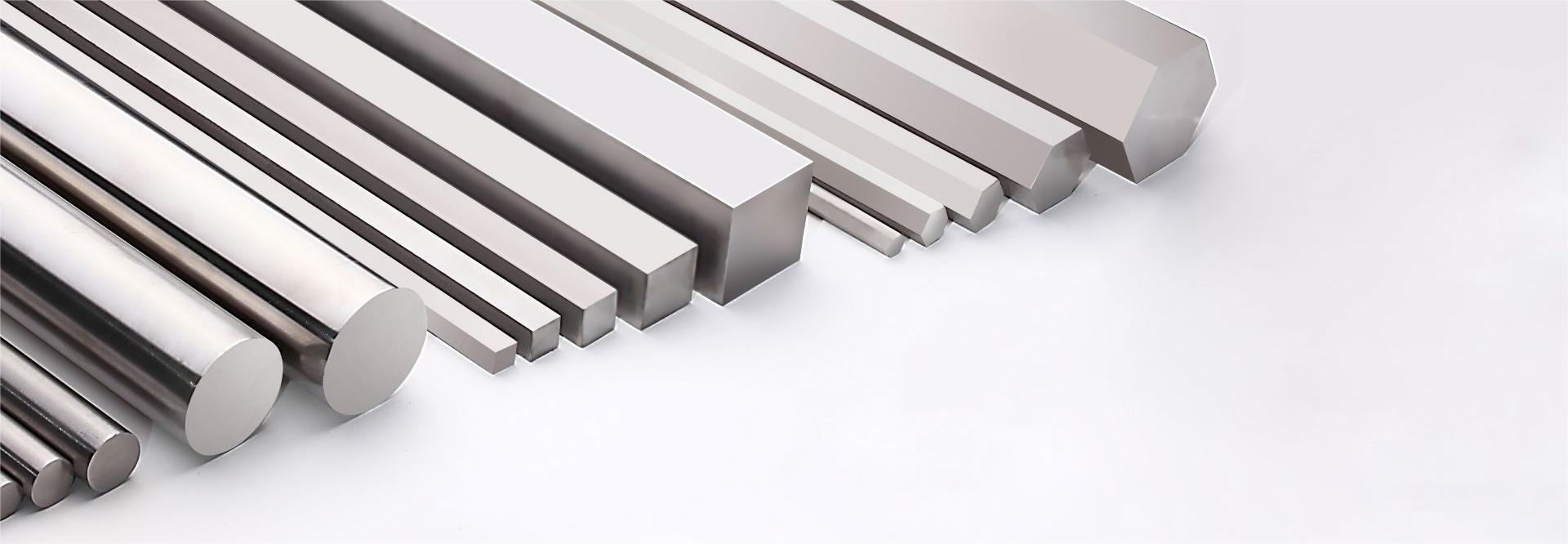
Marking and Inspection of Steel
2024-03-15 13:59(1) Logo A logo is a symbol that distinguishes the material and specifications of materials, mainly indicating the supplier's name, brand number, inspection batch number, specifications, size, level, net weight, etc. The logo has; 1. Color coating: Apply various colors of paint on the end faces and ends of metal materials, mainly used for steel, pig iron, colored raw materials, etc. 2. Printing: The method of stamping or painting on the designated parts (end face, end) of metal materials, explaining the material's grade, specifications, standard number, etc. Mainly used for medium and thick plates, profiles, non-ferrous materials, etc. 3. Tagging: Metal materials such as bundles, boxes, and shafts are labeled outside to indicate their brand, size, weight, standard number, supplier, etc. The marking inspection of metal materials should be carefully identified and properly protected during transportation, storage, and other processes. (2) Inspection of specifications and dimensions Specification size refers to the nominal size of the main parts (length, width, thickness, diameter, etc.) of a metal material. 1. Nominal size: It is the ideal size that people want to obtain in production, but it has a certain difference from the actual size. 2. Size deviation: The difference between the actual size and the nominal size is called size deviation. A deviation greater than the nominal size is called a positive deviation, and a deviation less than the nominal size is called a negative deviation. Within the specified range of the standard, it is called allowable deviation. If it exceeds the range, it is called size deviation. Deviation is considered unqualified product. 3. Accuracy level: The allowable size deviation of metal materials is specified in several ranges, and is divided into several levels according to the different allowable size deviation, which is called accuracy level. The accuracy level is divided into ordinary, higher, advanced, etc. 4. Delivery length (width): refers to the main dimensions of metal material delivery, which refers to the length (width) specification that the metal material should have at the time of delivery. 5. Normal length (indefinite length): There is no specific regulation on the length, but it must be within a specified length range (depending on the variety and length, determined by the department or factory). 6. Short ruler (narrow ruler): The length is less than the lower limit of the specified normal length dimension, but not less than the specified minimum allowable length. For some metal materials, a portion of the "short ruler" can be handed over according to regulations. 7. Fixed length: The length of the metal material submitted must have the length specified by the purchaser in the purchase contract (generally positive deviation). 8. Double length: The length of the metal material to be delivered must be an integer multiple of the length specified by the purchaser in the purchase contract (including saw edge and positive deviation). The inspection of specifications and dimensions should pay attention to measuring the material location and selecting appropriate measuring tools. (3) Inspection of quantity The quantity of metal materials generally refers to the weight (except for a few cases where pads and fishplates are counted in pieces), and the quantity inspection methods include: 1. Measurement by actual weight: Metal materials measured by actual weight should generally be fully weighed and inspected. For solid packaging (such as boxes, containers, drums, etc.), gross weight, net weight, and tare weight should be indicated on the packaging. For example, thin steel plates, silicon steel sheets, and ferroalloys can be sampled for at least 5% of a batch. If the sampled weight differs significantly from the marked weight, all samples must be opened and weighed. 2. According to theoretical conversion measurement: The weight calculated based on the nominal size (actual size) and specific gravity of the material can be converted according to theory for materials such as fixed size plates. However, when converting, attention should be paid to the conversion formula and the actual specific gravity of the material. (4) Surface quality inspection Surface quality inspection mainly refers to the inspection of materials, appearance, shape, and surface defects, mainly including: 1. Ellipticity: The phenomenon in which a metal material with a circular cross-section has unequal diameters in all directions on the same cross-section. Ellipticity is represented by the difference in diameter between the maximum and minimum on the same section, with different material standards for different purposes. 2. Bending, bending degree: Bending is the rolling of materials. A general term for an uneven or curved shape in the direction of length or width. If their unevenness is expressed in numbers, it is called curvature. 3. Twisting: The strip rolled material is twisted into a spiral shape along the longitudinal axis. 4. Sickle Bend (Side Bend): Refers to the bending of metal plates, strips, and shapes with a rectangular cross-section along their length (narrow side), with one side forming a concave curve and the other side forming a convex curve, known as the "Sickle Bend". Represented by the concave height. 5. Piao curvature: refers to the wave phenomenon that occurs simultaneously in the length and width direction of a board or strip, forming a Piao curvature shape, called Piao curvature. The numerical value that represents the degree of curvature is called the degree of curvature. 6. Surface crack: refers to the crack on the surface of a metal object. 7. Ears: protrusions that extend along the rolling direction due to improper matching of rolling rolls and other reasons are called ears. 8. Gouge: Refers to the straight or curved grooves on the surface of the material, which can usually be seen at the bottom of the grooves. 9. Scar: refers to a thin, uneven distribution of tongue like, nail like, or fish scale like flakes on the surface of a metal material. 10. Bonding: The mutual adhesion between layers, lines, and surfaces of metal plates, foils, and strips during rolling and annealing, which leaves bonding marks on the surface after being lifted, is called bonding. 11. Iron oxide scale: Iron oxide scale refers to the metal oxide formed on the surface of a material during heating, rolling, and cooling processes. 12. Folding: A surface defect formed during the hot rolling process (or forging) of a metal, with a bimetallic layer that folds together in a straight or curved shape. 13. Spot: refers to the rough surface of a metal material that is uneven. 14. Subcutaneous bubbles: The surface of metal materials exhibits irregular distribution, varying sizes, shapes, smooth small protrusions around, and ruptured protrusions with chicken claw shaped cracks or tongue shaped scars, which are called bubbles. The main causes of surface defects are improper operations such as production, transportation, loading and unloading, and storage. Depending on the impact on usage, some defects are not allowed to exceed the limit at all. Some defects may not exist, but they are not allowed to exceed the limit; Whether and to what extent various surface defects are allowed to exist are clearly specified in relevant standards. (5) Guarantee conditions for internal quality inspection The inspection of the internal quality of metal materials is based on the adaptation of the material to different requirements, and the guarantee conditions are also different. During the factory and acceptance, the inspection must be carried out according to the guarantee conditions and meet the requirements. The guarantee conditions are divided into 1. Basic guarantee conditions: The minimum requirements for material quality, whether or not proposed, must be guaranteed, such as chemical composition, basic mechanical properties, etc. 2. Additional guarantee conditions: Refers to the items that are inspected according to the requirements specified by the purchaser in the purchase contract, and ensure that the inspection results meet the requirements. 3. Agreement guarantee condition: The project that is negotiated and guaranteed by both the supply and demand parties in the purchase contract. 4. Modification conditions: The inspection items will be negotiated by both parties, but they are only for reference and not for assessment. The internal quality inspection of metal materials mainly includes mechanical properties, physical properties, chemical properties, process properties, chemical composition, and internal organization inspection, which are generally carried out by professional inspection institutions.