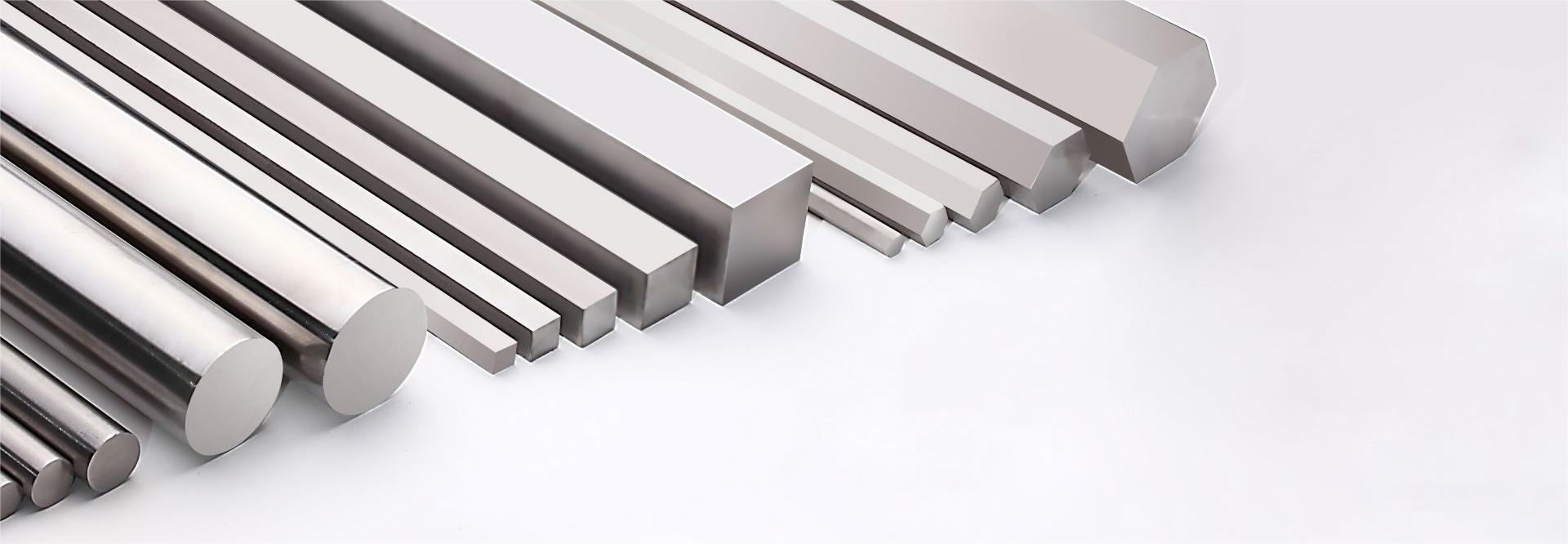
Comparison of Welding Performance between Low Carbon Steel and High Carbon Steel
2024-03-06 16:50The welding performance of steel mainly depends on its chemical composition. The carbon element has the greatest impact, which means that the amount of carbon in a metal determines its weldability. Most of the other alloying elements in steel are also not conducive to welding, but their impact is generally much smaller than that of carbon.
Low carbon steel generally has good weldability and does not require special process measures. It is only necessary to use alkaline welding rods for welding at low temperatures, thick plates, or when there are high requirements, and to preheat appropriately. When the carbon and sulfur content in low-carbon steel is above the upper limit, in addition to requiring the use of high-quality low hydrogen welding rods, preheating and post heating measures, it is also necessary to reasonably choose the groove form and reduce the fusion ratio to prevent the occurrence of hot cracks.
When welding medium carbon steel, there is a tendency for cold cracking. The higher the carbon content, the greater the tendency for quenching in the heat affected zone, the greater the tendency for cold cracking, and the poorer the weldability. As the carbon content of the base material increases, the carbon content of the weld metal will also correspondingly increase. In addition, the adverse effect of sulfur can easily form hot cracks in the weld. Therefore, alkaline welding rods with good crack resistance should be used for welding medium carbon steel, and measures such as preheating and post heating should be taken to reduce the tendency of cracks.
When welding high carbon steel, due to the high carbon content of this steel, significant welding stress is generated during welding. The hardening and cold cracking tendency of the welding heat affected zone is greater, and the weld seam is also more prone to hot cracks. High carbon steel is more prone to hot cracks during welding than medium carbon steel, so this type of steel has the worst weldability. Therefore, it is not used in general welding structures and is only used for casting repair welding or overlay welding. After welding, the welded parts should undergo tempering treatment to eliminate stress, fix the structure, prevent cracks, and improve the performance of the weld seam.